Тектонический процесс: как цифровизация изменит нефтяную отрасль
Нейронные сети, цифровые двойники, искусственный интеллект. Технологии "Индустрии 4.0" изменят нефтяную отрасль до неузнаваемости
Архитекторы цифровой эпохи
Обычно самыми технологичными принято считать сферы информационных технологий и биомедицины. К компаниям традиционных отраслей, занимающимся, например, металлопрокатом или добычей и переработкой нефти, отношение совсем другое. На первый взгляд они кажутся консервативными, но именно их многие эксперты называют главными архитекторами новой цифровой эпохи.
Автоматизировать производственные процессы индустриальные гиганты начали еще в середине 30-х годов прошлого века. На протяжении многих десятилетий комплексы аппаратных и программных средств непрерывно совершенствовались и усложнялись. Автоматизация производственных процессов - например, в нефтепереработке - продвинулась далеко вперед. Работу современного нефтеперерабатывающего завода контролируют сотни тысяч датчиков и приборов, а поставки топлива в режиме реального времени отслеживаются системами спутниковой навигации. Каждый день средний российский НПЗ производит более 50 000 терабайт информации. Для сравнения, 3 миллиона книг, которые хранятся в цифровом хранилище Российской государственной библиотеки, занимают в сотни раз меньше - "всего" 162 терабайта.
Это и есть те самые "большие данные", или Big Data, - поток, сравнимый с информационной загрузкой самых крупных сайтов и социальных сетей. Скопившийся массив данных представляет собой уникальный ресурс, который может быть использован в управлении бизнесом. Но традиционные методы анализа информации для этого уже не подходят. По‑настоящему эффективно работать с таким объемом данных возможно лишь с помощью технологий Индустрии 4.0. В условиях меняющейся экономической парадигмы богатый производственный "исторический опыт" - серьезное преимущество. Большие данные лежат в основе искусственного интеллекта. Его способность обучаться, понимать реальность и прогнозировать процессы напрямую зависит от объема загруженных знаний. При этом промышленные компании обладают мощной инженерной школой, активно занимаются внедрением и совершенствованием новых технологии. Это еще одно обстоятельство, которое делает их ключевыми игроками "новой экономики".
Наконец, отечественные промышленники знают цену эффективности бизнеса. Россия - страна больших расстояний. Нередко производственные активы находятся на большом удалении от потребителей. В этих условиях очень непросто быстро реагировать на колебания рынка. Традиционные технологии позволяют экономить не больше десятой доли процента. А между тем, цифровые решения уже сегодня позволяют сокращать издержки до 10−15% в месяц. Факт очевиден: в эпоху четвертой промышленной революции конкурентоспособным будет тот, кто научится наиболее эффективно применять новые технологии в разрезе накопленного опыта.
Петр Казначеев, директор Центра сырьевой экономики РАНХиГС: "В качестве первого шага в сторону "интегральной" системы искусственного интеллекта в нефтегазе можно было бы рассмотреть "умное" управление и корпоративное планирование. В данном случае речь могла бы идти о создании алгоритма оцифровки всей ключевой информации о деятельности компании - от месторождения до бензоколонки. Эта информация могла бы поступать в единый автоматизированный центр. На основе данной информации с помощью методов искусственного интеллекта могли бы делаться прогнозы и рекомендации по оптимизации работы компании".
Лидер цифровой трансформации
Осознавая эту тенденцию, индустриальные лидеры России и мира перестраивают бизнес-процессы, складывавшиеся десятилетиями, внедряют в производство технологии Индустрии 4.0 на основе промышленного интернета вещей, искусственного интеллекта и Big Data. Наиболее интенсивно трансформация происходит в нефтегазовой индустрии: отрасль динамично "цифровизируется", инвестируя в проекты, которые еще вчера казались фантастикой. Заводы, управляемые искусственным интеллектом и способные прогнозировать ситуации, установки, подсказывающие оператору оптимальный режим работы - все это уже сегодня становится реальностью.
При этом задача-максимум заключается в том, чтобы создать систему управления добычей, логистикой, производством и сбытом, которая объединила бы "умные" скважины, заводы и автозаправки в единую экосистему. В идеальной цифровой модели, в тот момент, когда потребитель нажимает на рычаг заправочного пистолета, аналитики компании в оперативном центре мгновенно получают информацию о том, какая марка бензина заправляется в бак, сколько нефти нужно добыть, поставить на завод и переработать, чтобы удовлетворить спрос в конкретном регионе. Пока что никому из российских и зарубежных компаний не удавалось построить такую модель. Однако дальше всех в решении этой задачи продвинулась "Газпром нефть". Ее специалисты сегодня реализуют ряд проектов, которые в итоге должны стать основой для создания единой платформы управления переработкой, логистикой и сбытом. Платформы, которой пока нет еще ни у кого в мире.
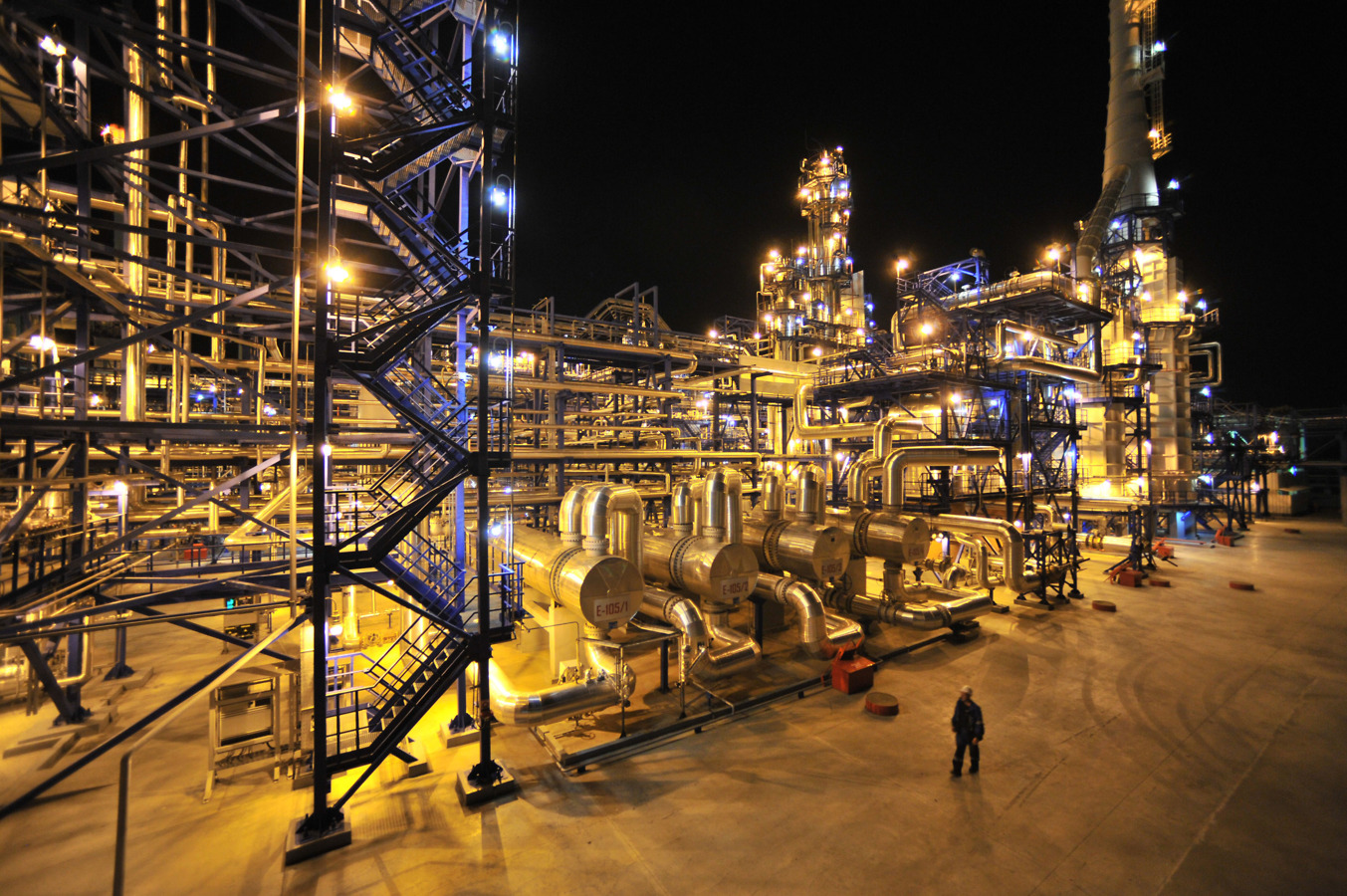
Цифровые двойники
На сегодняшний день НПЗ "Газпром нефти" являются одними из самых современных в отрасли. Однако четвертая промышленная революция открывает качественно новые возможности, одновременно предъявляя и новые требования к автоматизации. Точнее, речь идет не столько об автоматизации, сколько о практически полной оцифровке производства.
Основой нового этапа станут так называемые "цифровые двойники" - виртуальные копии установок НПЗ. В 3D-моделях достоверно описаны все процессы и взаимосвязи, происходящие в реальных прототипах. В их основе лежит работа искусственного интеллекта на базе нейронных сетей. "Цифровой двойник" может предлагать оптимальные режимы работы оборудования, прогнозировать его отказы, рекомендовать сроки ремонта. Среди других его плюсов - способность постоянно обучаться. Нейросеть сама находит ошибки, исправляет и запоминает их, улучшая тем самым свою работу и точность прогноза.
Базой для обучения "цифрового двойника" служит массив исторической информации. Современные установки нефтепереработки также сложны, как и организм человека. Сотни тысяч деталей, десятки тысяч датчиков. Техническая документация для каждой установки занимает помещение размером с актовый зал. Чтобы создать "цифрового двойника", всю эту информацию необходимо для начала загрузить в нейронную сеть. Затем начинается самый сложный этап - этап обучения искусственного интеллекта понимать установку. В него входят показания датчиков и контрольно-измерительных приборов, собранные за последние несколько лет работы установки. Оператор моделирует различные ситуации, заставляет нейронную сеть отвечать на вопрос "что будет, если поменять один из параметров работы?" - например, заменить один из компонентов сырья или увеличить энергоснабжение установки. Нейросеть анализирует опыт прошлых лет и методом вычисления исключает из алгоритма неоптимальные режимы, и учится прогнозировать будущую работу установки.
"Газпром нефть" уже полностью "оцифровала" два промышленных комплекса, задействованных в производстве автомобильного топлива - установку гидроочистки бензинов каталитического крекинга на Московском нефтеперерабатывающем заводе и установку, работающую на нефтеперерабатывающем заводе компании в Омске. Испытания показали, что искусственный интеллект способен одновременно учитывать огромное количество параметров их "цифровых двойников", принимать решения и оповещать о возможных отклонениях в работе еще до того момента, когда неприятность грозит перерасти в серьезную проблему.
Одновременно с этим "Газпром нефть" тестирует комплексные решения, которые позволят минимизировать влияние человеческого фактора в масштабах целого производства. Подобные проекты сейчас реализуются на битумных заводах компании в Рязани и Казахстане. Удачные решения, найденные опытным путем, впоследствии можно будет масштабировать до уровня больших НПЗ, что в итоге позволит создать эффективную цифровую платформу управления производством.
Николай Легкодимов, руководитель Группы консультирования по перспективным технологиям КПМГ в России и СНГ: "Решения, которые моделируют различные узлы, агрегаты и системы известны и применяются достаточно давно, в том числе и в нефтегазовой индустрии. О качественном скачке можно говорить лишь тогда, когда достигнута достаточная широта охвата этих моделей. Если удастся сочетать эти модели друг с другом, объединить их в целую сложную цепочку, то это, действительно, позволит решать задачи на совершенно новом уровне - в частности, моделировать поведение системы в критических, невыгодных и просто опасных условиях работы. Для тех сфер, где переоснащение и модернизация оборудования обходятся очень дорого, это позволит предварительно апробировать новые компоненты".
Управление эффективностью
В перспективе вся цепочка добавленной стоимости в блоке логистики, переработки и сбыта "Газпром нефти" будет объединена единой технологической платформой на базе искусственного интеллекта. "Мозгом" этого организма станет Центр управления эффективностью, созданный год назад в Санкт-Петербурге. Именно сюда будет стекаться информация от "цифровых двойников", здесь она будет анализироваться и здесь же, на основе полученных данных, будут приниматься управленческие решения.
Уже сегодня, в режиме реального времени более 250 тыс. датчиков и десятки систем транслируют информацию в Центр со всех активов компании, входящих в периметр блока логистики, переработки и сбыта "Газпром нефти". Каждую секунду сюда поступают 180 тыс. сигналов. Человеку только на просмотр этой информации потребовалось бы около недели. Цифровой мозг Центра делает это моментально: в режиме реального времени отслеживает качество продукции и количество нефтепродуктов по всей цепочке - от выхода с НПЗ до конечного потребителя.
Стратегическая же цель Центра в том, чтобы, используя технологии и возможности Индустрии 4.0, радикально повысить эффективность сегмента downstream. То есть не просто управлять процессами - это можно делать и в рамках традиционных систем, а сделать эти процессы наиболее эффективными: за счет прогнозной аналитики и искусственного интеллекта на каждом этапе бизнеса сокращать потери, оптимизировать процессы и предотвращать убытки.
В ближайшее время Центр должен научиться решать несколько ключевых задач, влияющих на эффективность управления бизнесом. В том числе прогнозировать будущее на 60 дней вперед: как поведет себя рынок через два месяца, сколько нефти нужно будет переработать, чтобы удовлетворить спрос на бензин в актуальный момент времени, в каком состоянии будет оборудование, смогут ли установки справиться с предстоящей нагрузкой и нужен ли им ремонт. При этом в ближайшие два года Центр должен выйти на 50%-ную мощность и начать отслеживать, анализировать и прогнозировать количество запасов нефтепродуктов на всех нефтебазах и ТЗК компании; в автоматическом режиме мониторить более 90% параметров производства; анализировать надежность более 40% технологического оборудования и разрабатывать мероприятия, предупреждающие потери нефтепродуктов и снижение их качества.
К 2020 году "Газпром нефть" ставит цель выйти на 100% возможностей Центра управления эффективностью. Среди заявленных показателей - анализ надежности всего оборудования, предупреждение потерь по качеству и количеству продукции, предиктивное управление технологическими отклонениями.
Дарья Козлова, старший консультант VYGON Consulting: "В целом интегрированные решения приносят существенный экономический эффект для отрасли. К примеру, по оценкам Accenture, экономический эффект от цифровизации может составить более 1 трлн $. Поэтому когда речь идёт о крупных вертикально-интегрированных компаниях, то внедрение интегрированных решений весьма оправдано. Но оно и оправдано для небольших компаний, так как повышение эффективности может высвободить им дополнительные средства за счёт снижения затрат, увеличить эффективность управления оборотным капиталом и т. д.".
|